Concrete is one of the most commonly used building materials in the world due to its durability, fire resistance and sturdiness. However, it can get damaged easily and may require repairs if not repaired on time.
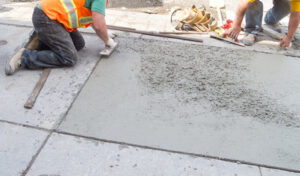
Regular repair activities can increase safety, extend the lifespan of the concrete structures and prevent major damage.
Concrete is used all over the world for countless applications, and it’s often exposed to harsh environments that can damage or degrade it. Roots can push concrete sections out of alignment, freeze-thaw cycles cause deterioration, and normal wear and tear from traffic can lead to discoloration. Using the proper repair techniques ensures the safety, longevity, and visual appeal of concrete structures.
The first step in the process is surface preparation. It’s essential to remove any contaminated or incompatible material from the concrete surface and prepare the area for the application of new concrete repair materials. This can include coatings, paint, or chemical contaminants that could impact the performance of the repair materials or prevent them from adhering to the concrete.
This is also the time to take note of any existing conditions that should be addressed. If there are any areas of the concrete that have been damaged or weakened by corrosion, it’s important to identify these areas and correct them before proceeding with the repair. It’s also a good idea to review any structural components, such as post-tension cables and electrical conduits, that are embedded in the concrete. These must be protected against corrosion to avoid the risk of failure or injury.
In addition to identifying existing problems, it’s important to understand what kind of cracking or surface defects are in the concrete. This will help determine what type of repair material is required. Common types of concrete damage include plastic-shrinkage cracks, which are thin in width and distributed throughout the concrete surface. These cracks occur as concrete is curing because of differences in the rate of shrinkage between the surface and the concrete below. Hairline cracks are much narrower in width and usually deep. These cracks are caused by settling of the concrete during the curing process or as a result of environmental changes.
Most concrete repair products require surface preparation to ensure that the bond between the old and new concrete is strong enough. Typically, this involves cleaning the area of loose concrete and applying a bonding agent. This step is especially important if you’re planning to use a mortar or masonry product. Liquid bonders like SpecChem’s Strong Bond or SpecWeld serve as the “glue” that helps to ensure the new concrete adheres to the existing concrete. They should be applied when they are still tacky, and ideally, it’s best to apply them directly to the concrete rather than mixing them into the water to ensure proper penetration.
Crack Diagnosis
Concrete surfaces are subject to a number of stresses including weathering, heavy foot and vehicle traffic, vibrations and settlement. These stresses can lead to damage to the surface, which may manifest as cracking. Whether the damage is cosmetic, structural or both, it is essential to address concrete problems promptly and efficiently. Failure to do so can lead to deterioration of the concrete surface and serious structural damage that will require costly repairs.
There are a number of different concrete repair methods, each with its own benefits and limitations. Surface repairs are generally used for minor surface damage such as cracks and spalling. These repairs are not intended to be structural and may need to be reapplied regularly as the patching material can wear down with time. Structural repairs are designed to provide a permanent repair and should be carried out by qualified professionals to ensure the structural integrity of the concrete structure is maintained.
It is important to identify the cause and type of the crack before beginning the concrete repair process. A thorough inspection will allow a professional to determine the correct repair method. This will ensure the long-term durability and performance of the repaired surface. The professional will also be able to advise on preventative maintenance techniques to help reduce the likelihood of future damage.
The first thing that must be identified is whether the crack is active or dormant. A crack that is at risk of growing or moving will be considered active and require immediate attention, whilst a dormant crack may still be a problem but is stable and will benefit from waterproofing and sealing.
An experienced concrete repair contractor will be able to identify the cause and type of cracking and recommend the most suitable repair method for the individual situation. They will also be able to advise on preventative measures that can be taken to minimise the chance of future damage to the concrete surface.
A quality concrete repair contractor will be able to provide a fast, cost-effective and durable solution for all types of concrete cracks and damage. They will use high-quality materials and equipment to provide a seamless, long-lasting finish.
Repair Materials
Concrete repair requires selecting the right material and applying it at just the right time to ensure that the damage doesn’t worsen. The best choice is usually to use a one-part material that is easy to work with. There are a lot of options, however, so you have to figure out what your specific needs are. What type of crack or problem are you trying to repair? Will it be structural, spall or cosmetic? Once you have a good understanding of what the issue is, then you can select a repair material.
Cement-based repair materials are typically used to repair damaged concrete structures. These include ordinary Portland cement mortar and grout, latex modified Portland cement mortar or concrete, quick setting non-shrink mortar and polymer concrete. Each has different characteristics that can be useful for particular applications.
Some of the key properties to look for in a repair material are its shrinkage (to avoid debonding from the concrete matrix), its freeze-thaw resistance and its ability to allow water vapor transmission. Other considerations include the flexural strength and abrasion resistance of the material. Lastly, the material should be compatible with the existing concrete in terms of its chemical composition and surface conditions.
Many research efforts have been directed at improving the bond between repair materials and the substrate concrete. This is because the effectiveness of repairs is often dependent on the interfacial interface between the two materials. [1]
In order to increase the bond strength, the surface of the old concrete should be prepared to create a mechanical interlock with the repair material. This can be done by sandblasting, grinding or shot blasting. [2]
Moreover, the characterization of the interface microstructure between concrete repair materials and the substrate is necessary to understand why some repair materials fail. To this end, a number of tests are available. These include flexural test (bend and monolithic failure mode), shear test, slant shear test and pull-out test. In addition, a non-destructive impact-echo technique has been developed to assess the adhesive property of the repair interface.
Installation
Concrete repairs help lengthen the lifespan of structures and surfaces that are subject to a lot of wear-and-tear. These repairs can be a much cheaper and quicker option than replacing the concrete altogether. However, there are situations when replacement would make more sense, such as deep cracks, major damage, or if the concrete is very old and shows signs of extensive degradation.
A condition evaluation is the first step in determining the cause of deterioration and selecting repair methods and materials. The evaluation can involve a review of the design and construction documents, a structural analysis of the structure in its deteriorated condition, destructive testing, nondestructive testing, and chemical and petrographic analyses of concrete samples.
It is also necessary to understand the environment in which the repaired structure will be located, such as interior or exterior; is the area subject to freezing and thawing cycles; will it be exposed to chemicals such as deicing salts; and any other factors that might affect the performance of the repair. This information will help determine the type of concrete repair material that is best suited to the environment in which the structure is operating.
When repairing concrete, the existing surface must be prepared properly. This will ensure that the repair adheres to the old concrete and does not delaminate. In order to do this, the damaged surface must be thoroughly cleaned and etched to remove any dirt, oil, or other contaminants that may be present. It is recommended that a specialized concrete surface cleaner be used for this purpose.
Once the surface is cleaned, it should be allowed to dry completely. If the repairs are to be done in warm weather, it is necessary to mist or spray the surface with water to hydrate the cement particles in the repair mixture and to minimize the permeability of the finished repair.
Many repair products claim to achieve high strengths very quickly, but these early strength gains come at a price. These products typically use aggressive ingredients that can lead to premature failure due to differential shrinkage and can result in a repair material that is less serviceable.